Everything you need to know about 3D Print an injection Mold
CNC machining is widespread for producing injection molds due to its high accuracy, precision, and stability. Yet, this procedure is time-consuming and expensive due to the need for skilled labor and long dedication to complete the job.
3D printing technology has all the solutions needed to bridge these gaps in CNC machining. Not only is it known for rapid prototyping but also for reducing production costs.
Using this technology, designers and manufacturers can 3D print an injection mold with complex configurations within hours without burning their pockets. Are you considering 3D-printed molds for your following projects? Please read the guide on how it can be effective for your business.
What Exactly 3D Printed Injection Mold?
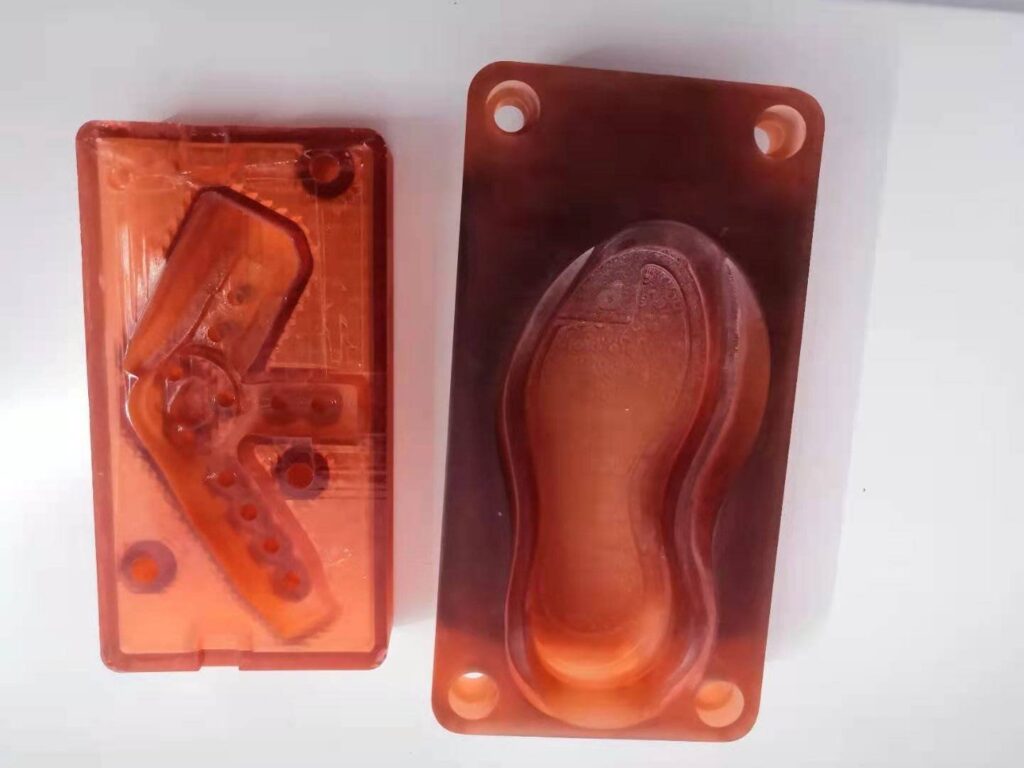
The 3D-printed injection mold is built from plastic polymers like ABS and polyethylene using one of the different 3D printing types. The selection of 3D printing types is based on mold features such as
- Physical and chemical properties of mold’s input resource.
- Strength and durability of the mold material.
Top 4 Benefits of 3D Printed Injection Mold
The 3D-printed injection mold is built from plastic polymers like ABS and polyethylene using one of the different 3D printing types. The selection of 3D printing types is based on mold features such as
- Physical and chemical properties of mold’s input resource.
- Strength and durability of the mold material.
A 3D-printed injection mold holds many advantages in terms of flexibility and is economical for your manufacturing project. It has more positive features that help you turn your business into a high-revenue model. Want to know about them? Step by step, read these characteristics of it.
Cheap in Making the Most
A 3D-printed injection mold is made from a plastic polymer that is cheaper than the aluminum and steel used in a CNC-machined injection mold.
Besides, average skilled labor can 3D print an injection mold without supervision. Both factors make this phenomenon affordable.
Minimum Knowledge is enough to Operate
The 3D printer works on CAD commands. There are no skills or expertise needed to fulfill its purpose. Connect your computer configuration to the printer and issue control to produce an injection mold.
Perfect for Low Quantity of Manufacturing
Mold-making using 3D printing technology needs minimal investment and affordable labor. It is why there is no requirement to produce a large quantity to cover the entire cost, just like in CNC machining.
Convenient and Flexible Procedure
3D-printed injection molds allow designers to customize post-development because they are built with soft materials like ABS and polyethylene.
Cons of 3D Printed Injection Molds
Every coin has two sides: positive and negative. The same can be said for 3D printed prototypes. Analyze these disadvantages one by one.
Deformation Issues
While cooling down 3D-printed components, they start shrinking and warping. It results in deformed dimensions and shapes in the final injection molds.
Defects in Structural Stability
3D-printed injection molds do not work for long-run production since they have weak structural rigidity. During the manufacturing of injection-molded parts, they lose their shape at consistently high temperatures and pressures.
Worthy Concerns for 3D Print an Injection Mold
The quality of a 3D-printed injection mold depends on its prior developmental parameters, like
- Quantity of print
- A suitable draught angle
- Uniform Finishing.
Quantity of Prints
3D-printed molds sound great only for short runs of approximately 30 to 100, as their plastic textures cannot hold consistent temperature and pressure. They are perfect for manufacturing lower-volume components compared to their counterparts, like aluminum and steel.
Draft Angle
The draught angle is the curved inner face of 3D-printed injection molds that aids in the complete ejection of the injection-molded parts. Professionals recommend that a 2-degree draught angle is enough to serve your business objectives.
Uniform Finishing
3D-printed injection molds have less surface integrity than metallic molds because high melting temperatures degrade their upper surface.
Because of its higher degradation, a ceramic sheath should be applied to the outer surface of a 3D printing injection mold if you want a uniform finish.