PA12, Best Material For Prototyping And Production By 3D Printing
What is PA 12?
One of the most useful kinds of plastics is nylon polymer. There are many different kinds of nylon polymers, and Polyamide 12 (PA 12), unsurprisingly, is a nylon polymer with 12 carbon atoms in it. This also explains its other commonly used name, nylon 12.
It’s a synthetic thermoplastic polymer. Thermoplastic materials become liquid at their melting point. For PA 12 the melting point is around 176 degrees celsius, the lowest of all Nylon polymers. There is some advantage to that. The lower the melting point, the easier it is to “print” the material. It helps the build not cool down too fast. Cooling too fast could cause warping.
What are the benefits of 3D printed PA 12?
Detailed parts
PA 12 is great for printing complex and detailed parts. This is mainly because there are no support structures needed during 3D printing. Support structures interfere with design freedom and are hard to remove, especially on small detailed surfaces. For PA 12, as long as the minimum wall-thickness of 0.8 mm is met, your options are virtually limitless.
PA 12 is really strong
This polymer is especially known for its resistance to cracking when under stress. Before it breaks it would bend, making this material really flexible. It’s tensile strength is 48MPa, flexural strength 41MPa and elongation at break is 18%.
Chemical resistance
PA 12 has outstanding chemical resistance to aliphatic hydrocarbons, oils, greases, ketones, and alkalies. Plus, it barely absorbs moisture.
Stability over longer periods of time
The material is especially stable over longer periods of time. We already mentioned some reasons but there’s more: like it being insensitive to cracking, it’s strength even below zero temperatures, hardness, resistance to abrasion and of course it being very chemically resistant. PA 12 also absorbs very little moisture. Because of that parts made from PA 12 are dimensionally very stable even when humidity levels fluctuate. It’s therefore ideal for applications where safety, durability or reliability over time is critical.
Combined with the enhanced design freedom inherent in 3D printing, PA 12 can be used for consumer goods, medical, industrial, aerospace, and other high-performance applications.
What about the Nylon PA 12 3D printing process?
PA12 parts could be built through MJF and SLS 3D printing technologies.
Both technologies are belong to the powder bed fusion family. Both processes build parts by thermally fusing (or sintering) polymer powder particles layer by layer.
The main difference between these two technologies is their heat source. SLS uses a laser to scan and sinter across each cross-section. MJF, on the other hand, dispenses an ink (fusing agent) on the powder for absorbing infrared light. The printer then passes an infrared energy source over the build platform to fuse the inked areas.
SLS printing is able to produce larger parts (up to 600 x 350 x 560 mm) than MJF printing (up to 380 x 284 x 380 mm). On the other hand, MJF can print features as small as 0.5 mm, while SLS can print a minimum feature size of 0.8 mm.
What surface quality can you get with SLS and MJF 3D printing?
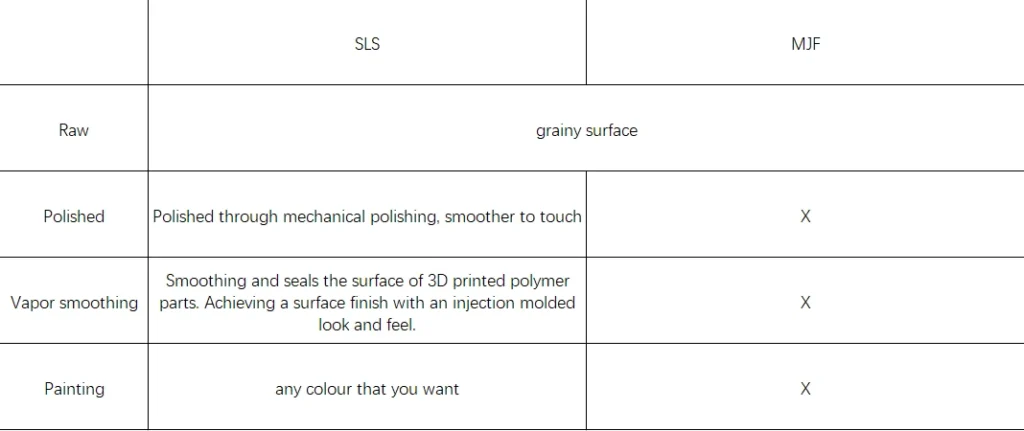
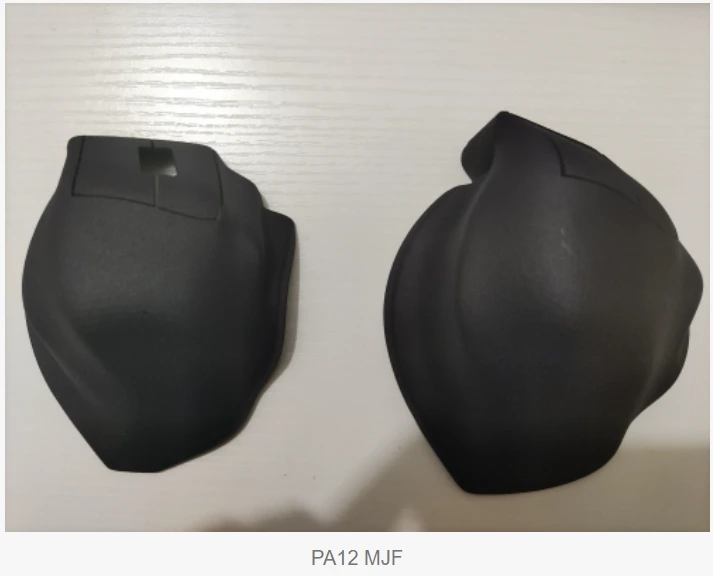
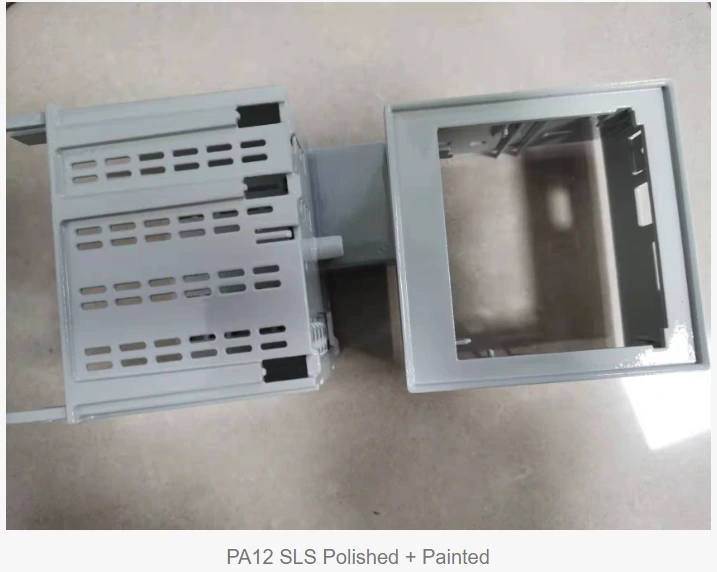