How to choose the right soft material?
Soft materials are around our lives, from common commercial uses including toys, ski boots, athletic shoes, to the medical industry including resuscitator parts, connectors, and mouthpieces, or to the automotive industry including floor mats, interior and exterior parts, and so on. We must have heard the names of these materials, but maybe we do not learn them closely.
Today’s topic, we will compare two groups of material. One group is TPE and TPU. The other is rubber and silicone. After reading, you will know the fundamental difference between two groups and the differences between two materials in one group, their applications and their molding processes. In the end you will know how to choose the right soft material for your product.
TPE and TPU
The difference between TPE and TPU
A thermoplastic elastomer is a type of thermoplastic polymer. Thermoplastics melt when heated above the material’s melting point and solidify when cooled. Because this melting process can be repeated many times, thermoplastics can be recycled. Thermoset polymers, on the other hand, cannot be melted again once they are formed. Silicone and synthetic rubber are thermosets.
Thermoplastic elastomers are thermoplastics with an elastomeric component that makes them soft and flexible. Although they can have a rubbery feel and are sometimes called thermoplastic rubber, they are not made out of rubber.
TPE (thermoplastic elastomer) and TPU (thermoplastic polyurethane) are among the most popular categories of thermoplastic elastomers — and while many use the terms interchangeably, they have some key differences. For starters, TPEs are a category encompassing a wide variety of thermoplastic elastomers while TPU only refers to a smaller subset. TPU is also newer to the manufacturing industry than TPE.
How TPE and TPU are defined is by their hardness, which measures a material’s resistance to surface deformation. As we know, TPU is harder than TPE, and TPU’s Shore hardness is between 60A and 55D.
Logically, TPE has a wider range of hardness than TPU. the hardness range of TPE can be chosen from shore hardness scale 0 to 100 of shore hardness. The variation in chemical formulation of TPE means some types of TPE are partially hard and suitable for something like a car tire, while other types are very rubbery, like a rubber band.
Other differences include that a TPU print will be heavier, because TPU is denser than other TPEs. TPU also has a smooth finish, while TPEs usually have a more rubbery texture. TPU has better resistance to abrasion than most TPEs, and TPU shrinks less than other TPEs.
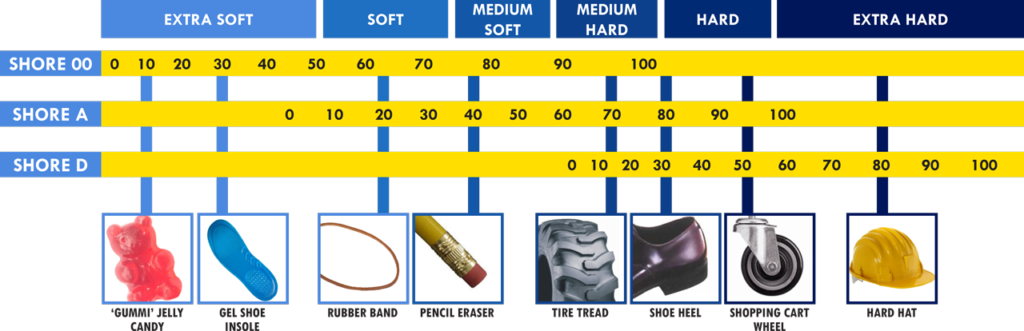
Applications
TPE is the polymer of choice for any application that must be soft to the touch and feature good elastic or non-slip properties. They are also ideal for applications in which a part must conform to a companion part. Common commercial uses for TPE include pencil grip handles, grips for hockey sticks, toys, and ski boots. In the medical industry, TPEs can be found in resuscitator parts, connectors, and mouthpieces. In the automotive industry, TPE is used in weatherproof seals, floor mats, interior and exterior parts, airbag covers, and bumpers.
TPEs do have a few limitations that product teams should keep in mind. For example, TPEs have been known to melt at extremely high temperatures and should only be used for parts whose uses will subject it to temperatures within the manufacturer’s specified temperature range. TPEs generally perform worse under heavy loads and have less chemical and temperature resistance than traditional thermoset rubbers.
TPU can be found in a wide cross-section of industries, from automotive, to agriculture, to textiles. The material’s unique combination of scratch and abrasion resistance makes it an excellent material for manufacturing automotive interior parts like gear knobs, instrument panels, or console parts. Its flexibility and breathability make it well-suited for sports apparel and athletic shoes. Some engineers have also developed niche TPUs to meet the increasing demand for high-performance polymers with low compression sets, abrasion resistance, and oil resistance for seals and gaskets.
Compared to polyvinyl chloride (PVC), TPU is lighter, more elastic, and more abrasion-resistant. It’s also possible to color and process TPU. It makes sense to choose TPU over PVC from an environmental standpoint because this material is recyclable and frequently used to lower carbon emissions. Also, TPU outpaces most other TPEs in a few key ways. TPU is generally harder, more durable, and more shrink-resistant than most TPEs — plus it is easier to print with and generally promises more accurate results.
Molding process
Since thermoplastic elastomers can be melted and reshaped without compromising the material’s chemical or mechanical properties, the scrap can even be re-used as a partial replacement for virgin plastic. Parts made from this material can be manufactured using a variety of processes, including vacuum casting, injection molding and 3D printing.TPE and TPU are available as filaments for use in FDM machines. 3D printing with TPE and TPU powders can also done through SLS machines.
Rubber and Silicone
The difference between Rubber and Silicone
Definition:Rubber is a tough elastic polymeric substance made from the latex of a tropical plant or synthetically. Silicone is a type of synthetic rubber.
Backbone structure: The backbones of most of the rubber forms contain carbon-carbon bonds. The backbone of silicone contains silicon and oxygen.
Properties: Rubber is usually less resistant to heat, chemical attacks, fungus attacks, UV and Ozone attacks. Silicone is more resistant to heat, chemical attacks, fungus attacks, UV and Ozone attacks than normal rubber.
Thermal insulation: Rubber is not much suitable due to less heat resistance. Silicone is much better than all other rubbers for thermal insulation due to its heat resistance.
Tensile and Tear properties: Organic rubbers have poor tensile and tear properties at high temperatures. These properties are excellent in silicone rubbers at the same temperature conditions.
Source: Rubber can be either natural or synthetic. Silicone is synthetic.
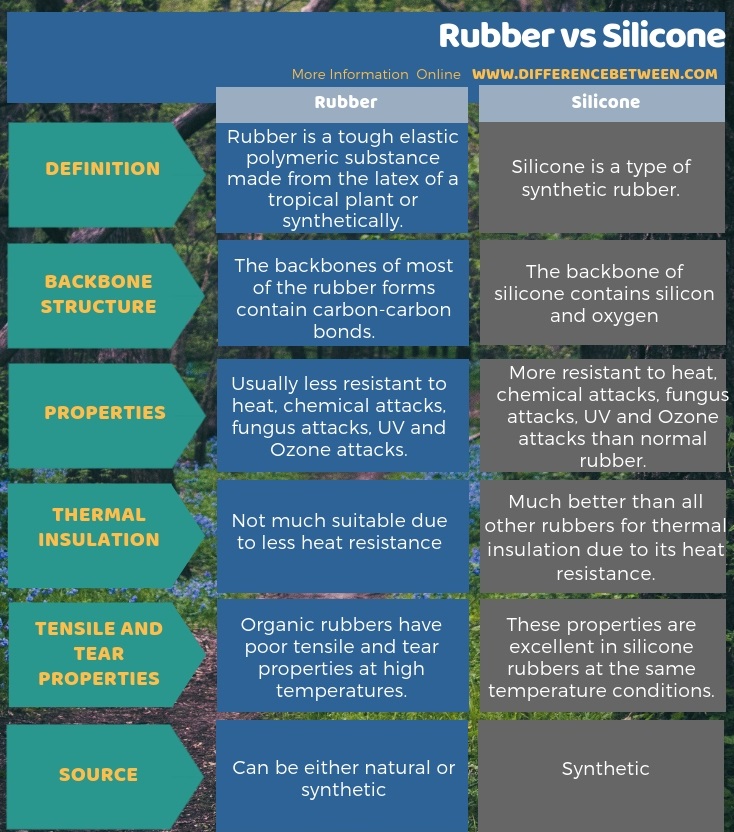
Molding process
Here are 3different sillicone molding processes: Compression Molding, Injection Molding and Extrusion Molding.
Comparison between TPE and Silicone
1.From processing performance perspective: Silicone needs to be molded through vulcanization, but TPE can be molded without vulcanization. Silicone is more difficult to be processed and molded, while the production and processing of TPE is simpler.
2.Silicone has an advantage over TPE in high temperature. The temperature resistance range of silicone is 200 ~ 300 ºC, while that of TPE is theoretically 130ºC ~ 150 ºC, and above that range, TPE will age and crack.
3.Prices of silicone rubber are higher than TPE. TPE has an advantage of being cheaper. Except for special TPE materials, silicon has such merits as halogen-free, flame retardant, food-grade proper, etc.
4.From cost perspective, silicone wastes cannot be recycled, whereas TPE wastes, nozzle residues and edge materials can be fully recycled and reused. Thus, TPE is more cost effective.