How to select the right CNC material and finish?
CNC Machining Materials
Since CNC Machining process is compatible with various of materials — from metal to plastic — it’s easy to mistakenly choose a sufficient material for the project but not the best suited. This article will discuss critical CNC machining material selection considerations and overview some standard options.
Aluminum alloys
It has an excellent strength-to-weight ratio, high thermal and electrical conductivity, and natural protection against corrosion. They are the most popular ones in CNC machining materials. They can be easily machined and have a low bulk cost, so they are often the most economical option for creating custom metal parts and prototypes.
Aluminum alloys typically have lower strength and hardness than steels, but they can be anodized, creating a hard, protective layer on their surface.
Stainless steels
It has high strength, high ductility, excellent wear, and corrosion resistance and can be easily welded, machined, and polished. Depending on their composition, they can be either (essentially) non-magnetic or magnetic.
Mild steels
Mild steels have good mechanical properties, machinability, and weldability. Due to their low cost, they find general-purpose applications, including the manufacturing of machine parts, jigs, and fixtures. Mild steels are susceptible to corrosion and attacks from chemicals.
Alloy steels
It contain other alloying elements besides carbon, resulting in improved hardness, toughness, fatigue, and wear resistance. It has good corrosion and chemical attacks.
Tool steels
Tool steels are metal alloys with exceptionally high hardness, stiffness, abrasion, and thermal resistance. They are used to create manufacturing tools (hence the name), such as dies, stamps, and molds. To achieve their good mechanical properties, they must undergo heat treatments.
Brass
It is a metal alloy with good machinability and excellent electrical conductivity, ideal for applications that require low friction.
ABS is one of the most common thermoplastic CNC machining materials offering good mechanical properties, impact strength, high heat resistance, and machinability.
Nylon, also known as polyamide (PA), is a thermoplastic often used for engineering applications due to its excellent mechanical properties, good impact strength, and high chemical and abrasion resistance. It is susceptible to water and moisture absorption, though.
Polycarbonate is a thermoplastic with high toughness, good machinability, and excellent impact strength (better than ABS). It can be colored, but typically it is optically transparent, making it ideal for a wide range of applications, including fluidic devices or automotive glazing.
POM is commonly known by the commercial name Delrin, an engineering thermoplastic with the highest machinability among plastics.
POM (Delrin) is often the best choice when CNC machining materials plastic parts that require high precision, high stiffness, low friction, excellent dimensional stability at elevated temperatures, and deficient water absorption.
PTFE is commonly known as Teflon and is an engineering thermoplastic with excellent chemical and thermal resistance and the lowest coefficient of friction of any known solid.
PTFE (Teflon) is one of the few plastics that can withstand operational temperatures above 200oC and is an outstanding electrical insulator. Nevertheless, it has pure mechanical properties, and it is often used as a lining or insert in an assembly.
High-density-polyethylene(HDPE) is a thermoplastic with a high strength-to-weight ratio, high impact strength, and good weather resistance.
HDPE is a lightweight thermoplastic suitable for outdoor use and piping. Like ABS, it is often used to create prototypes before Injection Molding.
PEEK is a high-performance engineering thermoplastic with excellent mechanical properties, thermal stability over an extensive range of temperatures, and excellent resistance to most chemicals.
PEEK is often used to replace metal parts due to its high strength-to-weight ratio. Medical grades are also available, making PEEK suitable also for biomedical applications.
Surface finishes are applied after machining and can change the appearance, surface roughness, hardness, and chemical resistance of the produced parts. Below is a quick summary of the most common finishes for CNC.
As machined
CNC machining produces a part with an “as-machined” or “as-milled” finish as soon as the manufacturing process is completed. The part will have small but visible tool marks and blemishes. The average surface roughness is around 3.2 μm. As-machined parts have the tightest dimensional tolerances and are incredibly affordable to produce because post-processing isn’t necessary.
This finish is a good choice for those who are more concerned with dimensional integrity than aesthetics. However, parts with as-machined finishes don’t rank very highly regarding protection. Their roughness and lack of protective coating render them susceptible to nicking, scuffing, and scratching.
Anodizing
Anodizing is an electrochemical process that thickens a CNC machine part’s natural oxide layer to make it thicker, denser, electrically non-conductive, and more durable.
During anodizing, the alloy is submerged in an acid electrolyte bath and acts as an anode. Once a cathode is placed in the anodizing tank and an electrical current passes through the acid, oxygen ions from the electrolyte and atoms from the alloy combine at the part’s surface. This process can only be done using aluminum or titanium alloys because they conduct electricity well.
Anodizing comes in two different varieties — Type II and Type III. The finishing process is the same, but Types II and III require that the part be submerged in a diluted sulfuric acid solution.
Anodizing Type II, also known as “decorative anodizing” (as the finished coating can be clear or colored), produces coatings up to 25 μm thick. The coating thickness range for clear parts is 4-8 μm and 8-12 μm for parts that have been dyed black. This process produces a part that is smooth, elegant, and resistant to corrosion and wear.
Anodizing Type III, also known as “hard coat anodizing,” can produce anodic coatings up to 125 μm thick. Parts with this coating have high density and are even more wear-resistant than anodizing Type II.
All in all, anodized finishes are durable and promise reasonable dimensional control. Anodized finishes are best used in high-performance engineering applications, particularly for internal cavities and small parts. They are among the most aesthetically pleasing finishes for CNC machined parts but often come at a higher price tag.

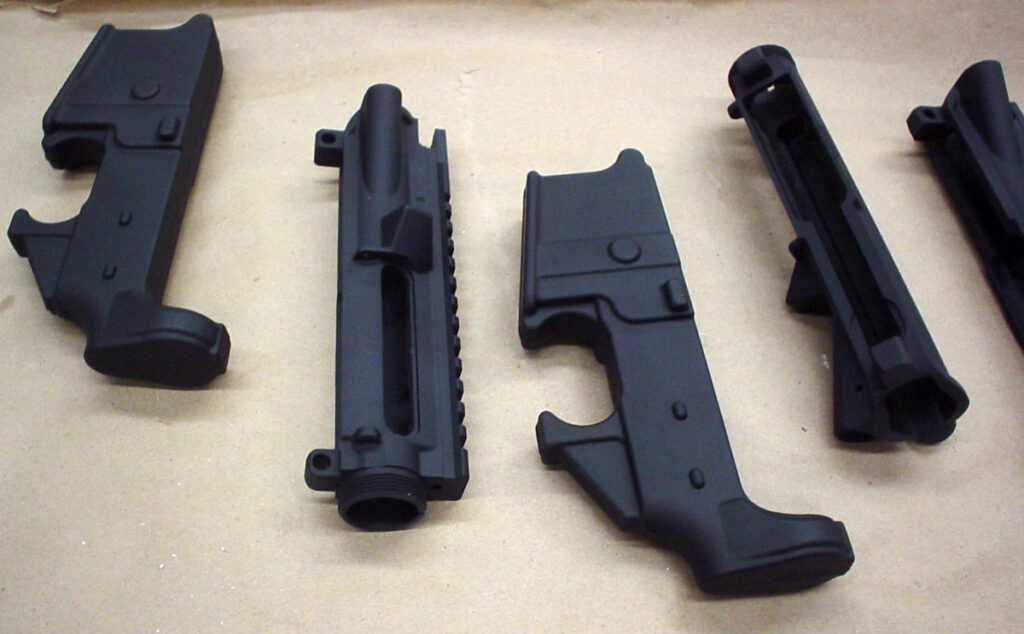
Powder coating is a lot like spray painting. First, the part is primed with a phosphating or chromating coat to make it more resistant to corrosion. Then, the part is “painted” with a dry powder coating from an electrostatic spray gun and cured in an oven heated to at least 200°C. Multiple layers can be applied to increase thickness, reaching 72 μm.
This finish creates a thin protective layer on the CNC machined part that is strong, wear-resistant, and aesthetically pleasing. This process can be combined with bead blasting to increase the part’s corrosion resistance and create more excellent uniformity in texture and appearance.
Unlike anodizing, a powder-coated finish is compatible with all metals, less brittle, and offers more excellent impact resistance. This finish is suitable for many functional applications but may be particularly well-suited for military applications.
However, powder coating generally yields less dimensional control than an anodic finish, and a powder coating is not recommended for use in small components or internal surfaces. Moreover, powder coating’s higher price point might make it prohibitively expensive for larger production runs.

Bead blasting
Bead blasting adds a matte or satin surface finish to a CNC machined part. During this process, a pressurized air gun shoots millions of glass beads at the part, effectively removing tool marks and imperfections and creating a consistent grainy finish.
Unlike powder coating, which adds material to a position, bead blasting is a reductive finish, meaning it removes material from the part. In contrast to other finishes, including anodizing and powder coating, bead blasting adds no chemical or mechanical properties to the part — it’s purely visual. This is an important consideration if your part has strict tolerances.
Bead blasting is one of the most affordable surface finishes, but it must be executed manually. As such, those considering bead blasting as a surface finish should be prepared to incur the cost of engaging an operator who has been formally trained in this process and recognizes that the final result will largely depend on how skilled the operator is. Bead size and grade will also affect the final finish.
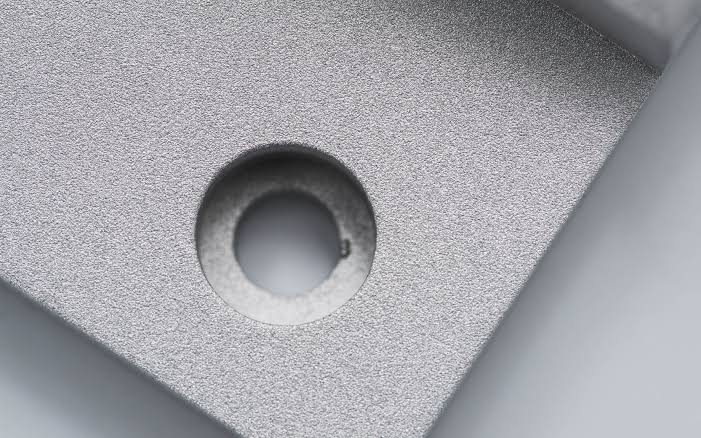
In short, a post-processing finish such as anodizing or powder coating will likely prove a practical option for parts that don’t need to be picture-perfect but must maintain their original dimensions. Protecting or reinforcing an aluminum or titanium part may benefit from anodizing. Powder coating provides a compelling alternative if the part cannot be anodized but requires strength and impact resistance.
Finally, if cost-effectiveness is a higher priority than tolerance — and the part does not require a glossy finish — bead blasting may be the preferable route.
IN3DTEC hope this article can help select the suitable CNC Machining materials and surface finishes.