Differences: Laser cutting, waterjet cutting, Plasma cutting and wire cutting
Laser Cutting
Laser cutting is to use the focused high-power laser to directly irradiate the product workpiece, so that the irradiated raw materials are quickly melted, vaporized, burned or reached the point of ignition, and at the same time rely on the high-speed cyclone output coaxially with the light to blow off the molten material, And then finish cutting the product workpiece. Nowadays, CO2 single-pulse laser generators are generally used, and laser cutting is one of the thermal cutting methods.
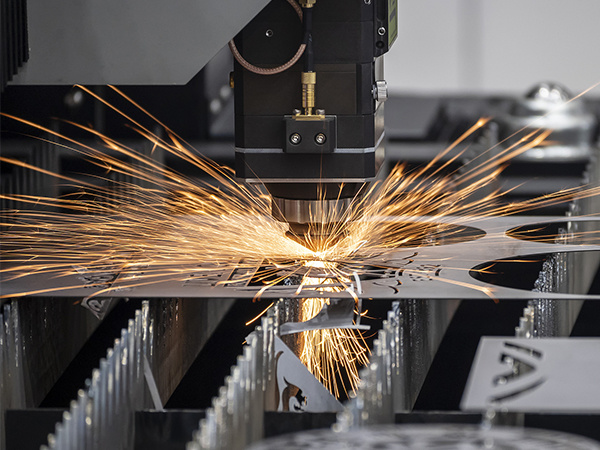
Waterjet cutting
Water cutting, also known as water jet, is a high-pressure jet-cutting technology, which is a device that uses high-pressure water cutting. Under the control of the computer, the product workpiece can be engraved at will, and it is less affected by the material quality. Water cutting is divided into two methods: no sand cutting and sand cutting.
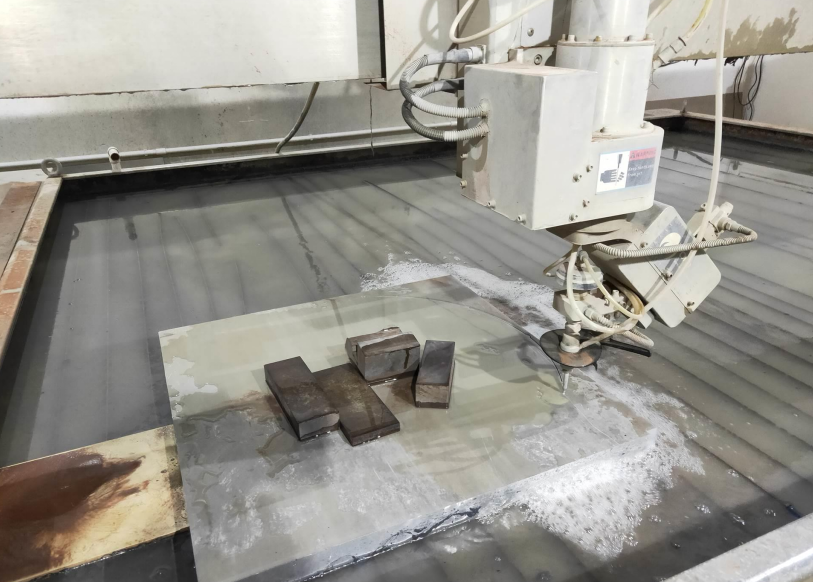
plasma cutting
Low-temperature plasma arc cutting is a process that uses the heat generated by high-temperature and low-temperature plasma arcs to partially melt (and volatilize) the metal material at the workpiece wound and removes the molten metal material by the angular momentum of high-speed low-temperature plasma to form a wound way.
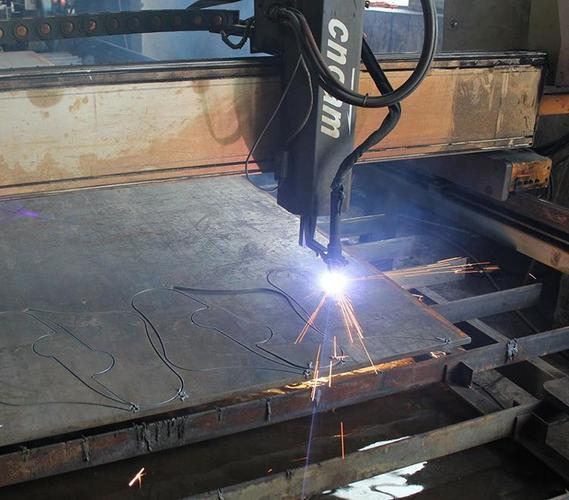
Wire cutting
Spark discharge wire cutting machine (Wirecut Electrical Discharge Machining, commonly known as WEDM), which belongs to the scope of metal processing, spark discharge wire cutting production and processing (Wirecut Electrical Discharge Machining, commonly known as WEDM), is sometimes called wire cutting. Wire cutting can be divided into fast wire cutting, medium wire cutting and slow wire cutting. The wire speed of fast-moving wire spark discharge wire cutting is 6-12m/s, and the wire electrode moves back and forth at high speed, and the cutting accuracy is weak. The medium-feeding wire-spark wire cutting is based on the fast wire-cutting to realize the DC frequency conversion multiple cutting function, and it is a new technology developed in recent years. The wire speed of slow wire spark discharge wire cutting is 0.1m/s, and the wire electrode performs unilateral movement at low speed, and the cutting accuracy is very high.
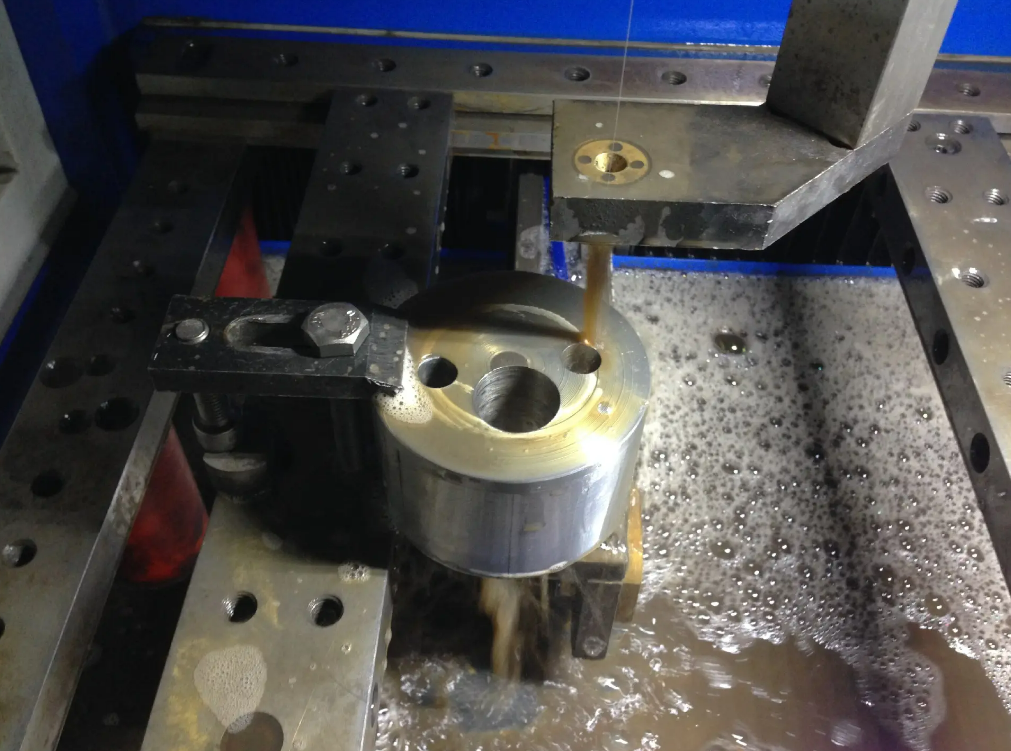
The laser cutting machine has a wide range of applications. It can cut metal materials and non-metal materials. CO2 laser cutting machines can be used to cut non-metal materials, such as fabrics and leather products. Fiber laser cutting machines can be used to cut metal materials. The deformation of the plate is small.
Waterjet cutting belongs to thermal cutting, jet deformation, high cutting surface, no need for secondary processing, and it is easy to carry out secondary processing if necessary. Waterjet cutting can open holes and cut all materials, with faster cutting speed and flexible processing specifications.
Plasma cutting machine can be used to cut various metal composite materials such as stainless steel, aluminum, copper, pig iron, carbon steel, etc. Plasma cutting has obvious thermoelectric effect, low precision, and the cutting surface is not easy to carry out secondary processing.
Wire cutting can only cut conductive substances, and coolant is required during the cutting process, so it cannot cut paper, leather and other materials that are non-conductive, waterproof, and afraid of coolant pollution.
Cutting thickness comparison:
The application of laser-cut carbon steel in industrial production is generally below 20MM. The cutting capacity is generally below 40MM. The industrial production and application of stainless steel plates are generally below 16MM, and the cutting capacity is generally below 25MM. And with the increase in the thickness of the product workpiece, the cutting rate is significantly reduced.
The thickness of water cutting can be thick, 0.8-100MM, or even thicker materials.
The plasma cutting thickness is 0-120mm, and the best cutting quality range is about 20mm. The low-temperature plasma system is the most cost-effective.
The thickness of wire cutting is generally 40-60mm, and the thickness can reach 600mm.
Cutting speed comparison:
Use a laser with an output power of 1200W to cut a 3mm thick high-carbon steel plate at a cutting speed of 600cm/min; cut a 5mm thick polypropylene resin plate at a cutting speed of 1200cm/min. The cutting efficiency that spark discharge wire cutting can achieve is generally 20 to 60 cubic millimeters per minute, and the Z maximum reaches 300 cubic millimeters per minute; obviously, the laser cutting speed is faster and can be used for mass production.
The speed of water cutting is very slow, and it is not suitable for large-scale mass production.
The cutting speed of plasma cutting is relatively slow, and the relative accuracy is low. It is more suitable for cutting thick steel plates, but the inner hole has a slope.
For the processing of metal materials, wire cutting has higher precision, but the speed is relatively slow. Sometimes it needs to use other methods to cut holes and wires to cut, and the cutting size is very limited.
Cutting accuracy comparison:
The laser cutting wound is thin and narrow, the two sides of the slit are parallel to the surface and vertical to the surface, and the specification accuracy of the cut parts reaches ±0.3mm.
Low-temperature plasma can achieve within a millimeter;
Water cutting will not cause thermal deformation, and the accuracy is ±0.mm. If a dynamic water cutting machine is used, the cutting accuracy can be improved, and the cutting accuracy can reach ±0.02mm, eliminating the cutting inclination.
The processing accuracy of wire cutting is generally ±0.01~±0.02mm, and the Z maximum reaches ±0.004mm.
Comparison of the overall width of the slot:
Laser cutting is more precise than plasma cutting, and the kerf is small, about 0.5mm.
The kerf of plasma cutting is larger than that of laser cutting, about 1-3mm;
The slit of water cutting is about 10% larger than the diameter of the knife tube, generally 0.8mm-1.3mm. As the diameter of the sand knife tube expands, the wound becomes larger.
The kerf width of wire cutting is the smallest, generally around 0.1-0.3mm.
Cutting process performance comparison:
The surface roughness of laser cutting is not as good as that of water cutting, and the thicker the material, the more obvious it is.
Water cutting always does not change the material of the raw material near the cutting seam (the laser belongs to thermal cutting, which will change the material near the cutting area.
IN3DTEC provides a full spectrum of technologies including 3D Scanning, Industrial 3D Printing, Reverse Engineering, CNC Machining, Vacuum Casting, Injection Molding, Die Casting, Laser cutting, plasma cutting, wire cutting and more manufacturing services