Topology Optimization for 3D Printing
Where does good design meet function? As computer-aided design (CAD) continues to evolve and advanced manufacturing techniques like 3D printing become more widespread, making it possible to create complex parts easier than ever before, designers and engineers can leverage topology optimization software to push boundaries and find new ways to maximize design efficiency.
In this guide, learn about the basics of topology optimization, its benefits and applications.
How It Works
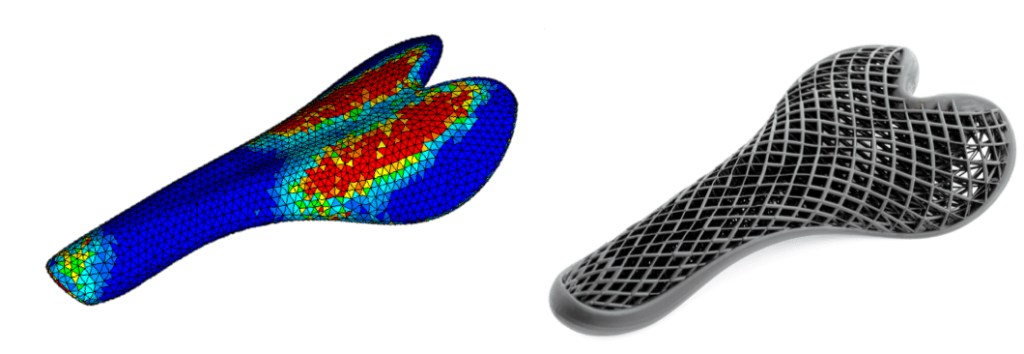
While there are many different topology optimization methods, perhaps the most practical are FE-based techniques. FE stands for finite element, which relates to the finite element method(FEM), yet another powerful numerical method widely used for mathematical and engineering problems. It’s the foundation of the computer-aided engineering (CAE) simulation software we know and use today.
In practical terms, TO makes use of finite element analysis (FEA) simulations to assess which areas of an object are not structurally crucial. The initial FEA simulates the stress distribution of an object submitted to external forces (previously inputted by the user). With these results, TO algorithms can verify which sections of the object are less subject to internal stresses and therefore potentially able to be removed.
The algorithm is constantly evaluating the structural stress distribution as it removes material, in order to assess the resulting effects. This is done through many individual steps until stable geometries are obtained according to the loadings and boundary conditions set up previously.
Topology optimization tools are generally used in a two-phase design process. The first run is usually performed to provide a glimpse of the optimal geometry and guide the user in the direction of the best design possible. The second run is more assertive in terms of final part detailing. This approach has proven to be very time-efficient, though time is only one of many advantages of this process.
The benefits of topology optimization
A faster design process
Topology optimization software helps to speed up the part development and design process by automatically iterating the design until it creates an optimized geometry.
By factoring performance requirements into the design right from the start and automating the design generation process, it’s possible to come up with an innovative design much faster, ultimately speeding up the design cycle.
Lighter and stronger parts
Perhaps the biggest advantage of using topology optimization is the ability to enhance part performance by reducing its weight and optimizing its strength.
By adding or removing the material in places, defined by a set of parameters, topology optimization tools allow engineers to explore endless design options and find the best possible a lightweight, yet resilient, structure of a given part.
Lighter parts are sought after by many industries. In aerospace, for example, lightweight components can significantly reduce aircraft fuel consumption, while in motorsports they can radically improve racecar performance.
Additionally, the lighter the part, the less material that has been used to produce it, which brings down manufacturing costs.
Applications of Topology Optimization
The high performance, efficient, and lightweight designs possible with topology optimization techniques apply across a wide range of industries.
Aerospace
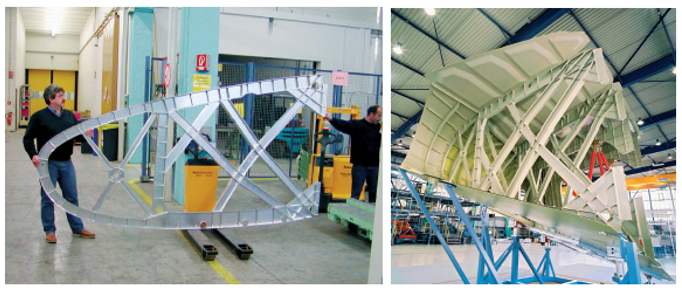
Due to the importance of weight reduction, topology optimization is a natural match for aerospace engineering and aeronautics. TO has been used, for example, to improve the layout design for airframe structures, such as stiffener ribs or brackets for aircraft.
Beyond enabling structural lightweighting, topology optimization can help unlock the potential of advanced manufacturing technologies like additive manufacturing or composite materials that are increasingly popular in the sector.
Automotive
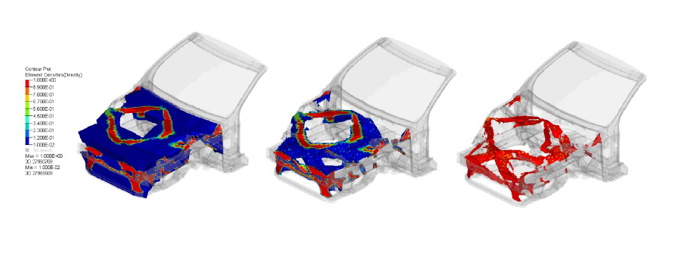
In the automotive industry, topology optimization balances the desirability of lightweight parts for fuel efficiency and power with the stability and strength of a body that can withstand torque and impact.
Besides mass savings, topology optimization can also improve passenger safety by defining the way a structure collapses during an accident.
Medical
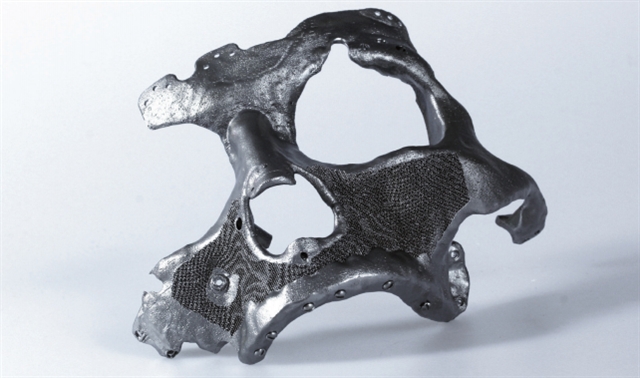
Additive manufacturing is ideal for creating medical implants, as it empowers medical professionals to create free-form shapes and surfaces, and porous structures. Thanks to topology optimization, the designs can feature lattice structures that are more lightweight, provide improved osseointegration, and last longer than other implants.
TO tools can also optimize the designs of biodegradable scaffolds for tissue engineering, porous implants, and lightweight orthopedics. Nanotechnology applications—such as cell manipulation, surgery, micro fluids, and optical systems—also use topology optimization.
Moving into the future, the capabilities of topology optimisation for 3D printing will continue to evolve, unlocking new, powerful possibilities.