What Is Mold Flow Analysis In Injection Molding?
Injection molding is a popular method for mass producing molded parts by injecting plastic materials with heat into a mold.
However, with time, manufacturers face issues after the production of molded parts, such as deformed shape, non-uniform surface, irregular thickness, and others.
Mold flow analysis in injection molding eliminates all problems by determining everything ahead of time. It identifies all risks and numerous variables associated with the critical component of production before the mold begins its functions.
It is a concise insight; here you are aware of a mold flow analysis and its merits in detail.
What is a Mold Flow Analysis in Injection Molding?
Mold flow analysis is a software-based simulation of how resin or molten material will flow inside the mold. It detects a variety of parameters that professionals must be aware of prior to do mass production. Such parameters are as
- Determine sink mark and short fill.
- Disclosure of material choke points and hot spots.
- Assess weld line.
- Calculate the number of gates and their locations.
and a variety of other topics required to optimize a mold design for regular molding operations.
Why is Mold Flow Analysis in Injection Molding Essential?
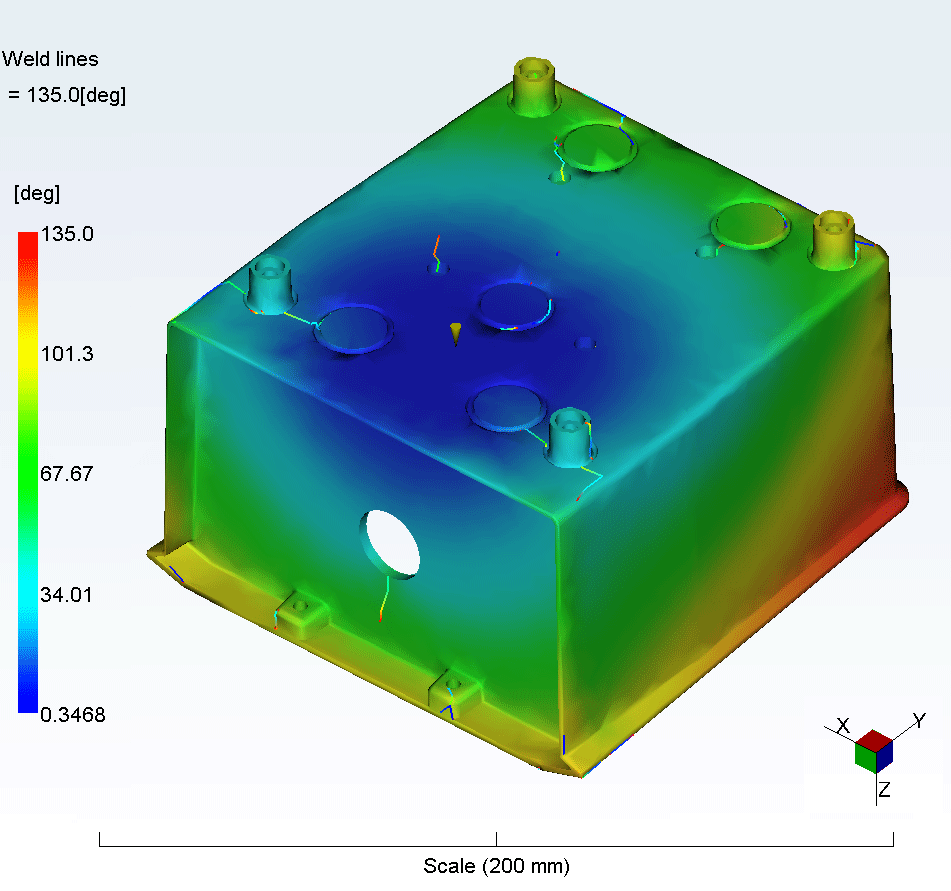
Mold flow analysis solves many conventional injection molding issues, so it is a vital tool for predicting manufacturing challenges.
- Shrinkage calculation for mold tolerances.
- Warpage anticipations
- Flow-induced shear stress.
- Mold and coolant temperature and pressure.
- Number of gates and their specifications.
- Other important handling conditions.
Merits of Mold Flow Analysis in Injection Molding?
The best feature of a mold flow analysis is that it analyses the whole performance of a mold before it kicks off. It allows manufacturers to shortlist the right material that has tolerable properties and select the gate area using software simulation.
It means that you are aware of everything beforehand about the operating conditions of your tool. In this way, you customize your tool fabrication too by selecting appropriate plastic materials and optimize its operating conditions. It is just a brief overview; apart from that, mold flow analysis has more merits in injection molding as
- Enhance quality and productivity
- Pour mold cavities consistently and properly.
- Lessen the mold design related mistakes and reworks.
- Determine the upcoming visual issues like air traps, sink marks, and weld lines.
- Build a robust or successful mold design.
- Identify a relevant plastic material for the desired results.
- Assess the relevant wall thickness
- Establish an optimize gate design.
- Figure out defects in mold geometry.
Conclusion
Mold flow analysis in injection molding has lots of benefits, which is the most important reason to have professionals look for it. It saves high costs and time delays by setting up deformation issues and analyzing how a mold performs and forms a molded part.
Such features enable manufacturers to control the quality and quantity of the resultant products.